
nVent Hoffman Hazardous Location Enclosures
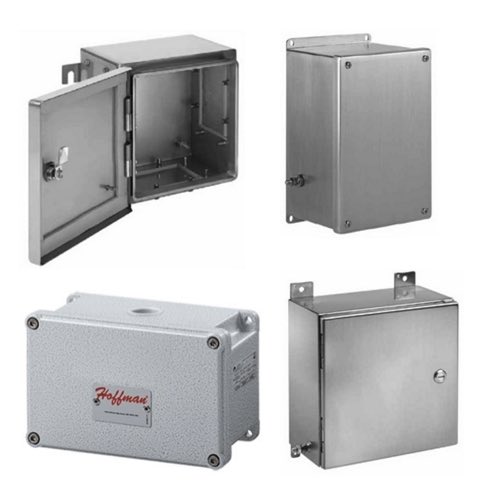
Hoffman hazardous location enclosures are crafted to keep electrical components safe in environments with flammable gases, vapors, or dusts. They're built tough to withstand the kinds of rigors that could pose real hazards in such locations and to meet standards like ATEX, IECEx, or UL that mandate " explosion-proof" construction around electric equipment that must serve such areas.
From the oil and gas industry to pharmaceuticals, a wide array of sectors relies on hazardous location enclosures. These protect mission-critical control systems, instrumentation, and personnel around them. The Hazardous Locations section of the National Electrical Code outlines requirements for electrical equipment installed in areas where there are high risks associated with fire or explosion hazards—specifically for medical purposes; doing so ensures that the dangers involved with these processes are minimized.
Products
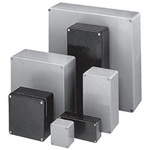
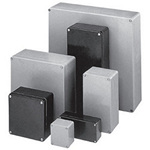
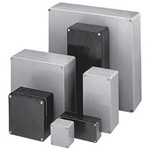
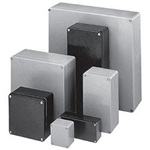

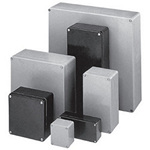

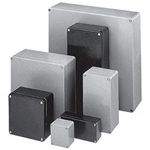
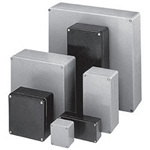
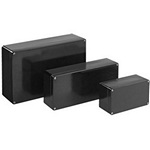
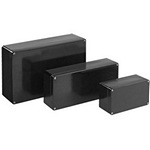
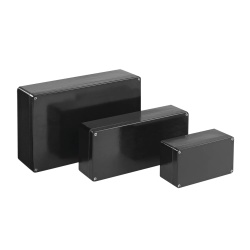
More Information about Hoffman Hazardous Location Enclosures
Class II enclosures are critical safety components in environments where combustible dust is present, providing robust protection for electrical equipment and ensuring compliance with safety standards to prevent explosions and fires. They require threaded holes at all conduit entrances in steel plate ends and heavy duty cover hinges. A fiber gasket can help ensure dust-tight enclosures.
FAQs
What NEMA rating is available in Class II division 1 enclosures?
Class II Division 1 enclosures typically have a NEMA rating of NEMA 7, NEMA 9, or NEMA 4X, ensuring they are suitable for hazardous locations with explosive dust environments and providing protection against corrosion and ingress of dust and water.
Can pilot lights be mechanically attached to the covers of hazardous location enclosures?
Yes, pilot lights can be mechanically attached to the covers of hazardous location enclosures, provided they are certified for use in hazardous environments and installed according to safety standards and regulations.
Purge System Basics
3 common reasons to use purge systems
They allow electrical enclosures to be installed in hazardous areas without the need for explosion proof enclosures.
They recycle the air inside of an enclosure, reducing the internal temperature.
They help reduce the effects of corrosion on components housed within the enclosure.
How does a purge system work?
Purge systems use incoming air from a supply line, solenoid valves, pressure gauges and pumps, to constantly maintain a positive pressure inside an enclosure. This prevents any flammable gases from entering the enclosure potentially causing an ignition event to occur. By maintaining a positive pressure within the enclosure, moisture and corrosive gases are also prevented from entering the enclosure and damaging components. Most purge systems will ensure that the air inside the enclosure is recycled a certain amount of times within a given time period. This air recycle function assists in maintaining a cooler temperature within the enclosure.