
Modicon M171-M172 Logic Controller

Schneider Electric PLC Processors are programmable automation controllers that function as the core of the customizable PLC built with processors, I/O modules, backplanes, power supplies, and optional networking. This modular approach allows for expansion and flexibility in the design of logic controllers and automation controllers for industrial control systems.
Schneider Electric Modicon M171/M172 Logic Controllers are Nano PLCs with a focus on HVAC and pumping control solutions. M171 controllers are designed for HVAC, pumping and refrigeration machines that are not in direct communication with building management systems. M172 controllers are designed for automation of HVAC, pumping and refrigeration machines that are connected to building management systems via communication networks such as LonWorks and BACnet. M171 and M172 controllers can handle small to very large machines and can be networked to handle large systems.
The controllers come in three different types. Modicon M171 Optimized Logic Controllers are for compact and simple machines and are the smallest programmable controller on the market. Modicon M171 Performance Logic Controllers are for BMS-connectable and complex machines. They provide I/Os, more memory, connectivity and an embedded web server. Modicon M172 Performance Logic Controllers are for large, connected machines and provide more performance, connectivity and scalability.
Products
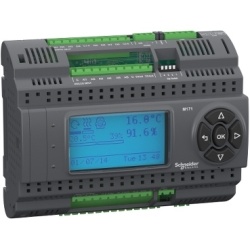
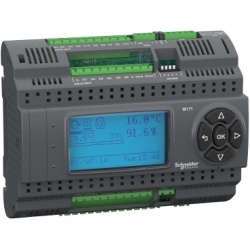
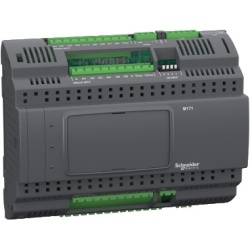
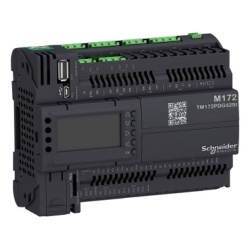
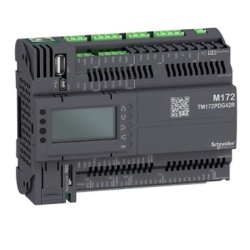
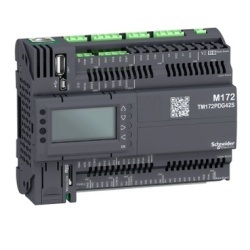
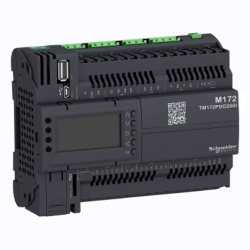
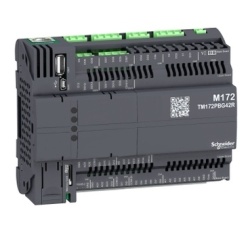
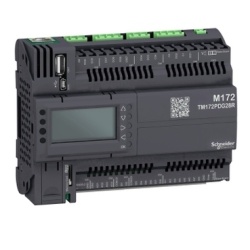
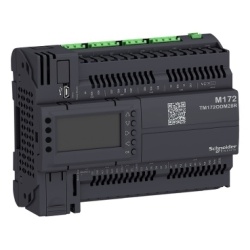
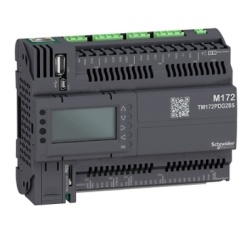
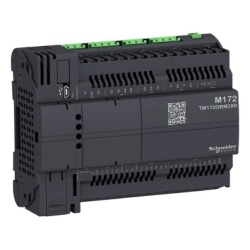
PLCs
Programming Logic Controllers (PLCs) are industrial computer that are designed to monitor and control a series of inputs and outputs.
The program running the PLC evaluates the inputs, and changes the output signals based on the program response to the input signals. Several programming languages are available to program most PLCs. The most common of these is called ladder logic. Ladder logic is a visual programming language that evolved from relay logic diagrams, which visually look like ladders because they consist of two vertical rails with runs between them that contain programmed logic. While ladder logic is the most common programming language used within PLCs, there are others that are also common, including function block diagrams, structured text and sequential function charts.
The hardware included in a PLC includes: a CPU, memory, I/O connections, a power supply and a programming device.
The CPU is a microprocessor that acts as the brains of the PLC. It performs logic operations, controls instruction and performs various other tasks that help keep the PLC running effectively. The memory in a PLC allows data to be stored that is needed to run the program, as well as any data that is collected by the inputs. Depending on the the type of PLC, the section for I/O may have a fixed number of points or it may be modular, allowing for additional I/O to be added. Many PLCs require some type of power supply and it is common to see more modular based systems integrate the power supply. Lastly, the PLC provides a programming device that feeds the program into the PLC's memory, so that it can perform the desired operation. This is most commonly some type of computer.
The PLC is designed to run a program repeatedly over and over again, normally many times a second. Each time a program runs, the PLC goes through some very specific steps.
While the order and the specifics may vary from manufacturer to manufacturer, they all typically follow a pattern similar to the following:
The PLC performs internal self checks to make sure that it is functioning correctly.
The PLC reads the inputs that are connected to it. It will then store the status of each of those inputs in its memory.
The PLC will execute the program logic.
The PLC will write the new values to the hard wired outputs to match those determined during the program execution. At some point in the cycle, communication requests will also be processed.
Following the execution of the last step, the PLC will then cycle back to the beginning of the process and begin all over again.