
Starter Accessories & Equipment
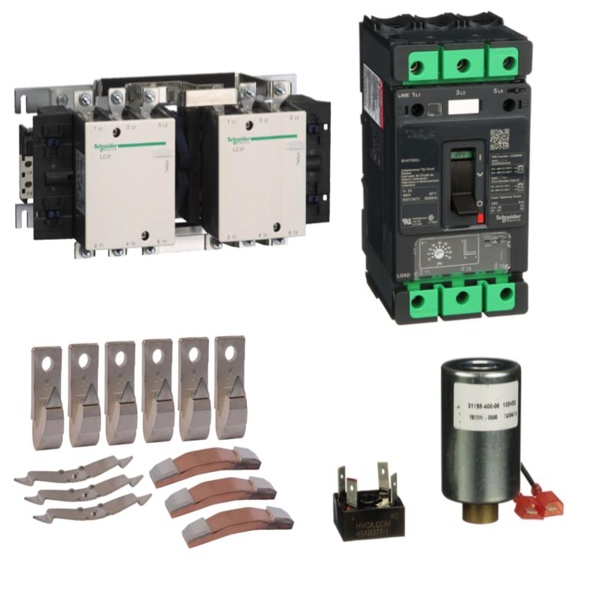
Contactor auxiliary contact blocks are used in a relay logic circuit typically switching 120 Volt AC power, instead of the motor voltage. A contactor is a relay that is used to switch a large amount of electrical power through its contacts. Contactors usually have multiple contacts that are normally-open, so that power to the load is shut off when the coil is de-energized. The most common industrial use for contactors is the control of electric motors.
Starter replacement coils are part of contactor used in the control of electric motors. When a contactor is closed, current flows to the coil (electromagnet) creating a magnetic coupling between contacts allowing current to flow to the motor. When de-energized, a spring causes the contacts to separate and stop the flow of power to the motor.
Starter thermal elements are part of thermal overload relays that indirectly measure motor heating by monitoring the amount of electrical current being delivered to the motor. Current flowing to the motor also flows through thermal overload relays by wiring them in series. When the current reaches or exceeds a preset limit, the relay activates a mechanism that opens one or more contacts to interrupt the current flow to the motor.
Starter disconnects and breakers are devices that work together to interrupt the flow of electricity along a circuit when an overcurrent occurs. Circuit breakers are designed to remove the current from a circuit when it exceeds a preset limit to prevent damage to connected devices. It does this automatically and immediately. A disconnect switch controls the flow of current to a circuit. It manually starts and stops power from an electrical supply by opening or closing an air insulation gap between two conduction points.
Products
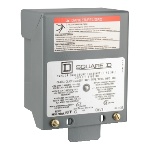
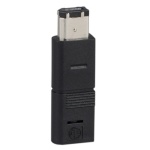
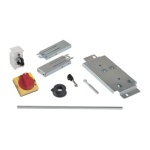
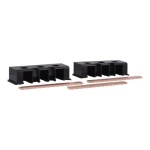
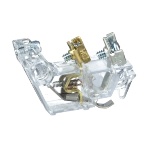
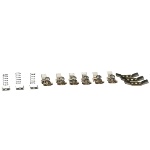
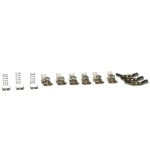

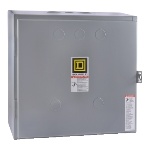
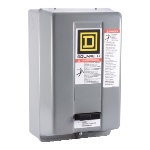
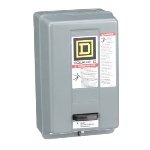
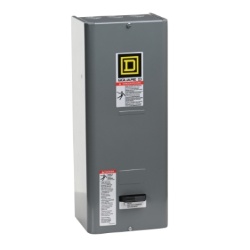
Motor Control Basics
Motor control allows operational control of electrical motors in various environments.
Motor control circuits provide a safe way to operate electrical motors. Back when motor control circuits were in their infancy, it would have been common to see a simple disconnect switch that would be used to turn on and off a motor. Depending on the size of the motor and how much voltage was required, operating this disconnect would have been dangerous, with a very high possibility of arcing or electrocution. Not to mention that when the disconnect was actuated, the large amount of inrush current would have damaged the motor over time.
In today's motor control circuits, there are a few common pieces of hardware.
A circuit breaker is used to protect the motor and any hardware downstream. A contactor and an overload relay are connected together and function in tandem to allow for remote and safe operation of the motor. The contactor functions much like a relay, allowing for a smaller electrical circuit to remotely close the motor contacts, starting the motor. The overload relay is designed to protect the motor in the case of a prolonged overcurrent event. These two devices are wired in series, so that if the overload relay detects an overcurrent event, the contactor will open the motor contacts, shutting off power to the motor.
The other two most common types of motor control hardware are a soft starter and a Variable Frequency Drive (VFD).
Both of these devices function in a similar way to the motor circuit with some added functions. The soft starter is designed to reduce large inrush current to the motor upon startup. This “soft starting” of the motor will prolong its life and allow for safer operation. The VFD performs the soft start functions, but also allows for speed control of the motor. This speed control is critical in many different environments and has made VFDs one of the most common and safe to use motor control circuits today.