
ZONEX Enclosure Accessories
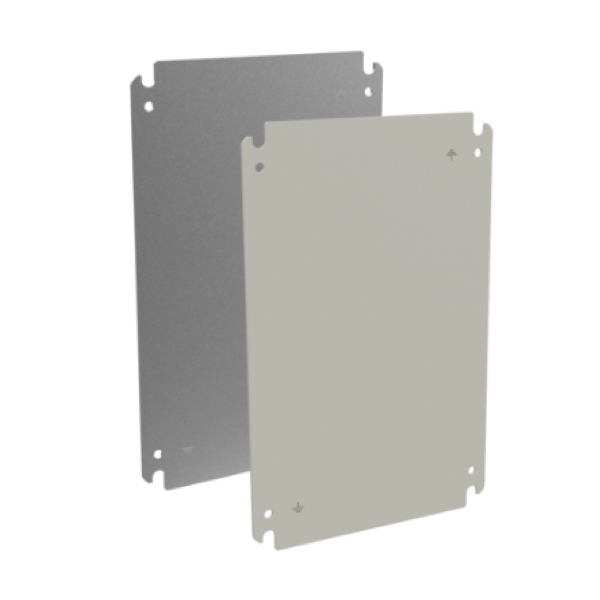
Hazardous location enclosures are specifically designed to isolate electrical components from hazardous locations. Hazardous locations are classified as areas where there is the possibility of explosion or fire because of the presence of ignitable or combustible gases, vapors, liquids, fibers or dust. Electrical equipment can be a potential source of ignition through sparks, equipment failure and high temperatures. Hazardous location enclosures are constructed to eliminate the potential for ignition of the atmosphere.
ATEX is a European Union directive from the European Committee for Standardization that covers protective systems and equipment intended for use in potentially explosive atmospheres. An atmosphere can be explosive for several reasons, including combustible dust, flammable gases, vapors or mists. All protective systems and equipment intended for use in the EU must meet ATEX health and safety requirements.
Products










More Information About ZONEX Enclosure Accessories
IECEx certification provides assurance that all safety requirements in the IEC standards are met and that both explosive atmosphere areas and the personnel working within them are as safe as possible.
Hoffman ZONEX enclosures are designed and certified to meet ATEX Directive 2014/34/EU as well as IECEx and AEx standards for increased safety in housing electrical components in Zone 1 and Zone 2 applications. Hoffman ZONEX ATEX back panels are designed for use with ATEX ZONEX enclosures. The 12 gauge steel panels provide a means to securely mount and install components inside the enclosure.
Panel Build Series 14: Drilling and Tapping
Drilling and tapping holes into a steel back plane for hardware attachment.
Take inventory of the tools needed for the job. A metal punch is used to make a small divot in the metal so that the drill bit won't wander, a very sharp machine drill bit and a 10-24 tap. The size of the bit and tap will depend on the type of hardware being used to secure the din rail and wire ducting to the panel.
Punch to create divots on previously marked layout. Always punch before drilling and make sure that the punch is in the center of the mark.
Drilling into the steel back plane. Make sure that the drill bit is very sharp, use lubrication to prolong the life of the bit, place the bit into the punched divot and start drilling. Clean up any metal shards when drilling is complete.
Tapping the holes to create threads. Make sure that the tap is very sharp and lubrication is used when tapping the holes. Do not over torque the tap which can cause it to break. Make sure that the tap goes completely through the hole until it turns easily to ensure that the holes have been properly threaded. Test the threaded holes with a screw. Clean up any metal shards. The back plane is now ready for mounting hardware.