
Pump Controllers
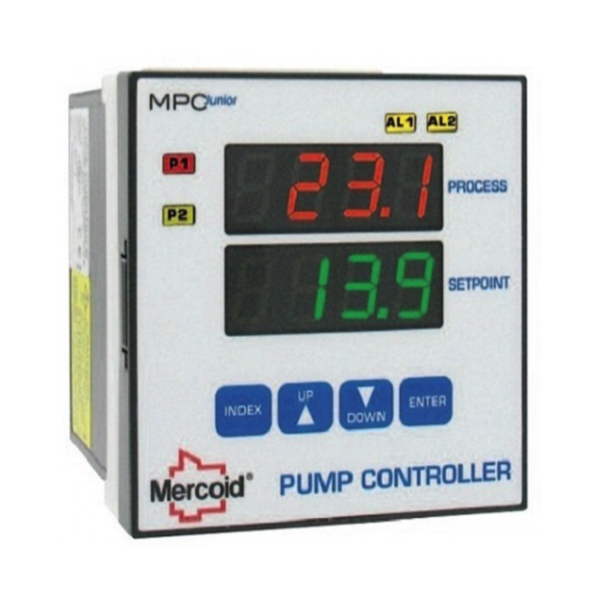
Pump controllers are devices used in various applications to control the operation of pumps. They receive signals, typically from level transmitters or other process variables, and provide outputs to manage the pump's operation. They play a significant role in pumping systems, such as those found in wastewater treatment facilities, irrigation systems, industrial processes, and more.
Pump controllers are usually designed to handle electrical power inputs, controlling the power delivered to the pump. In doing so, they monitor and maintain a desired process variable, such as the level of liquid in a tank or flow rate in a pipe.
The exact features and capabilities of a pump controller will vary based on the specific model and the application it's designed for. However, common features may include the ability to start and stop the pump, adjust pump speed, protect against conditions like dry running or overpressure, and provide diagnostic information. Some advanced controllers might also be equipped with features like automatic compensation for changes in flow or pressure, filtering of signal inputs, and more.
Products
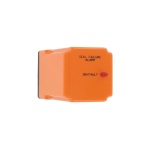
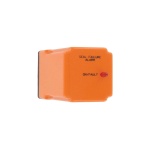
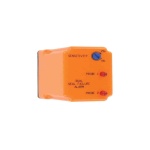
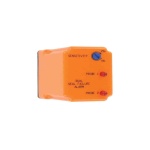
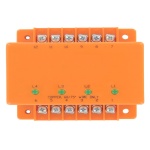
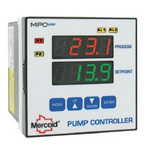
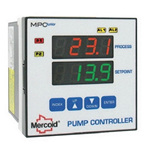
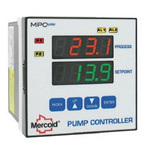
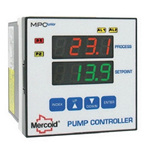
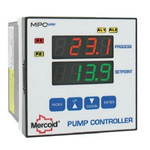
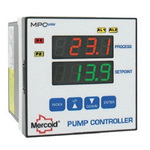
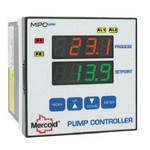
More Information about Pump Controllers
In the context of level control, a pump controller might be set up to start a pump when a tank level drops below a certain point, and stop the pump when the tank level reaches a desired upper limit. This could be accomplished using level transmitters that provide a signal to the pump controller.
Many pump controllers are built to operate in harsh environments and are equipped with features to support this, such as robust enclosures and protections against electrical faults.
It's important to note that pump controllers can be found in a wide variety of applications, from small domestic systems to large industrial processes. They are designed and built to meet the specific requirements of these applications, and there are many different models available to suit different needs.
Pump Curve Basics
What is a pump curve?
A pump curve is a graphical representation of the performance characteristics of a pump. This representation is typically shown as a graph with the “head” plotted on the x axis and the “flow” plotted on the y axis. Head is the height at which a pump can raise water. Connecting a tube or pipe to the discharge end of a pump and measuring the height at which the pump can raise the fluid, is the maximum head of the pump. Flow is the rate at which the fluid can be pumped through a pipe. With this information, the pump curve will display the most efficient way to use the pump.
What is the efficiency of a pump?
The efficiency of a pump is the relationship between the input horsepower required to drive the pump and the water horsepower created by the pump. The pump curve shows the optimal operating range and the allowable operating range. The optimal range is where the pump will perform at its peak, without putting too much stress on the pump. The allowable operating range shows where the limits of the pump are while still being able to safely function. It is best to operate the pump within the optimal range and not the allowable operating range.
What is the relationship between head and flow?
It is important to understand that head and flow are directly related to each other. For example, if a pump is expected to move 10 gallons of water per minute (GPM), the head will impact the flow rate at which the water can be pumped. If the pump is expected to move that water 50 feet upwards, it may not be able to achieve the necessary 10 GPM. It all depends on the pump design. If a pump is expected to move 10 GPM, with 3 feet head, it will be easier for the same pump to meet the expected 10 GPM.