
Polycarbonate Electrical Enclosures
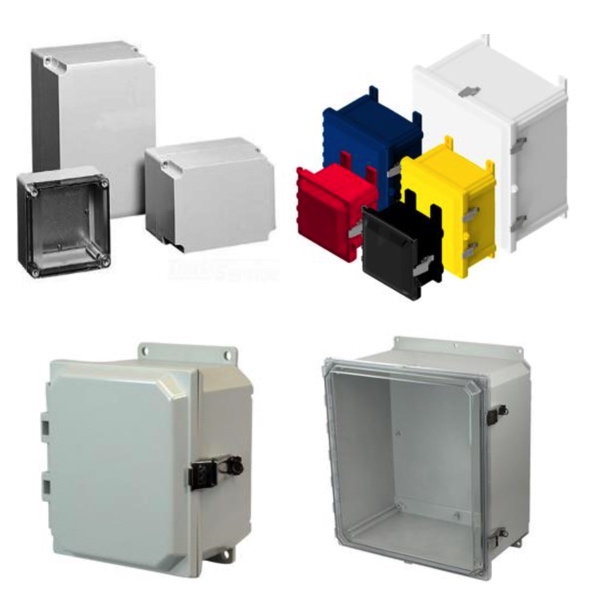
Electrical enclosures made of polycarbonate deliver significant protection for electrical controls and parts found both indoors and outdoors. The impact-resistant properties of polycarbonate, serving very well in industrial applications, must be explored along with other unique enclosure attributes, such as resistance to harsh outdoor environments. These enclosures resist UV exposure, they resist corrosion, and they resist physical impact.
Polycarbonate enclosures come in many sizes and configurations and offer versatile latching options. They're even UL listed to indicate that they meet safety standards that many consider to be stringent. The design of a polycarbonate electrical enclosure means that it is lightweight and yet durable, allowing for easy installation with low labor and material costs. They are found in a range of applications, from industrial automation to outdoor lighting systems, where they provide tough protection for the critical equipment inside that ensures operational continuity in the kinds of "bad" conditions that would disrupt most business operations.
Subcategories
Products
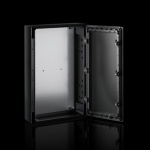
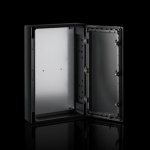
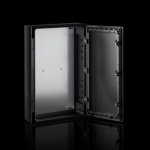
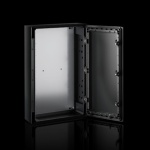
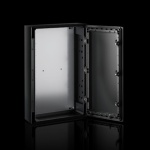
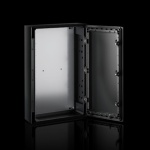
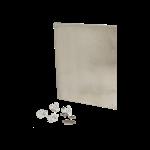
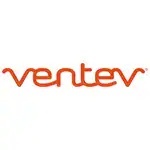

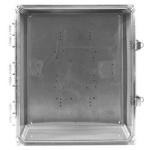
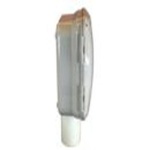
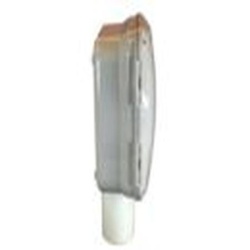
FAQs
Can Din rail be installed to the wall or panels of a polycarbonate enclosure to attach accessories?
Yes, DIN rails can be installed on the walls or panels of polycarbonate enclosures to securely attach accessories and instruments.
Non-Metallic Enclosure Types
Characteristics of non-metallic enclosures:
NEMA 4x rating for outdoor use providing chemical resistance and protection from dust, debris, water and rain.
High insulation value, which provides insulation from cold and hot temperatures, but does not dissipate heat from inside the enclosure.
Non-conductive, meaning components cannot be grounded to the enclosure, but it still provides the same security and tamper resistance levels as metallic enclosures when properly locked.
Types of non-metallic enclosures:
Fiberglass
A thermoset polyester material reinforced with glass fibers. It is the most widely used non-metallic material in the industry. It has high impact strength and rigidity (dimensional stability), a superior working temperature range (-31˚F to 300˚F), excellent electrical properties, moisture and chemical resistance, as well as being cost effective.
Polycarbonate
High-performance thermoplastic resin processed by injection molding or sheet extrusion. It is impact resistant, rigid (dimensional stability), has an extended temperature range (-31˚F to 180˚F), excellent electrical properties, fire retention, UV stability and corrosion resistance in some acidic surroundings. It is not suitable for environments with strong alkalis and organic solvents.
ABS or ABS blends
Acrylonitrile Butadiene Styrene is a common thermoplastic polymer processed by injection molding. It has high impact resistance, but less impact resistance in cold weather compared to polycarbonate, excellent electrical properties, superior chemical and moisture resistance, but a narrower temperature range than fiberglass (-40˚F to 248˚F).
Polyester
High-performance unfilled thermal plastic processed by injection molding. It has high impact resistance, but less impact resistance in cold weather than polycarbonate, excellent electrical properties, superior chemical and corrosion resistance, but a narrower temperature range than fiberglass (-40˚F to 248˚F).