
Capacitive Level Switches
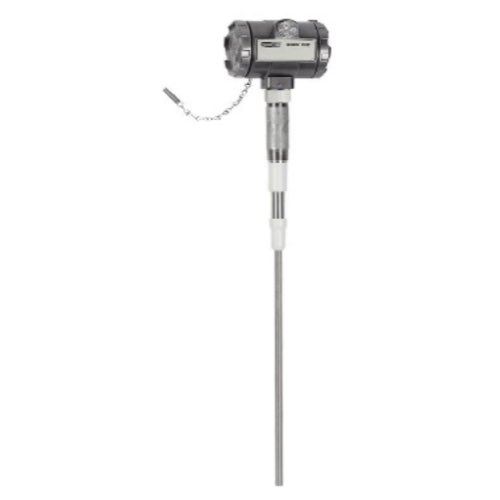
Capacitive level switches are widely used for point-level detection in various industries, providing reliable solutions for monitoring the presence of liquids and solids in tanks, silos, and bins. These switches operate based on capacitance change, where the probe detects variations in the dielectric constant of the media they are in, enabling them to accurately detect different materials—like water-based liquids, chemicals, and powders. Despite offering a more advanced technology than the mechanical switches that came before them, capacitive level switches are simple devices. They contain a probe and a few circuits, and they have no moving parts. They are maintenance-free, highly durable, and very versatile.
Capacitive level measurement technology allows services to take place and level detection to occur under difficult circumstances. These circumstances could range from having very humid or dusty conditions to having different parts of a system at very different temperatures. With easy installation in systems such as tanks or silos, these switches serve a few important functions. They help prevent the kind of dangerous dry run situations where a pump is running but there's not enough media in the way to do the job. They also help stop an overfilling situation from turning into an emptying situation.
Products


More Information about Capacitive Level Switches
Capacitive level switches come in many designs, including rod and cable probes, to fit various installation requirements and media characteristics. These sensors are installed in tanks or mounted on silo walls and are capable of very precise monitoring, even with media that have widely varying dielectric constants. They are used in industries like food and chemicals, where dielectric properties of the media might change because of the process, and they are selected often because of their durable, industrial designs. "With their robust design and advanced features, capacitive level switches continue to be a preferred solution for many industries seeking efficient and accurate level measurement.
Transmitters vs Transducers
Some of the most common types of transmitters and transducers can be found on pressure instruments. Examples of these include: drop-in well pressure devices and devices that measure the pressure in a pipe or gas chamber. Transmitters and transducers can also be found on flow and speed measurement devices.
What is the difference between transmitters and transducers?
The main difference is the way they send data to the monitoring device, like a PLC. In terms of measurement, the transmitter will reference a measuring unit by sending a milliamp signal (such as 4-20 mA). A transducer will reference a measuring unit by sending a voltage signal, typically in volts or millivolts.
Why have the two different types of transmission methods?
The method will depend on the application. If the electrical connection in the application travels a short distance, a pressure transducer is the better choice. Pressure transducers are smaller with fewer active electronic components that can be upset by electromagnetic interference. Also, the voltage signals transmitted over longer distances are subject to voltage drop and signal corruption. A transmitter is better for transmitting signals over a long distance.