
Modicon M340 & M580 Programmable Automation Controllers
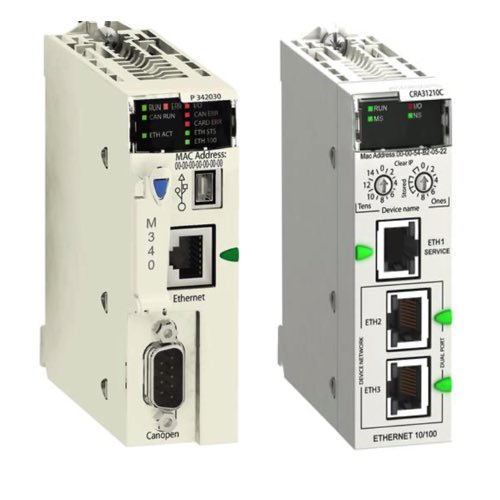
The Modicon M340 is a type of programmable logic controller (PLC) that is part of Schneider Electric's Modicon range. Designed for industrial applications, it offers a robust solution for automation needs across various industries including manufacturing, water treatment, and infrastructure. The M340 is well-regarded for its compact size, which makes it suitable for installations where space is at a premium, yet it doesn't compromise on performance or functionality.
This PLC is known for its high level of integration, allowing for seamless communication within complex systems. It supports a wide range of communication protocols, enabling it to connect with various devices and networks. This makes the Modicon M340 a versatile choice for systems that require integration with other automation components or need to support remote monitoring and control.
Programming the Modicon M340 is facilitated through Schneider Electric's Unity Pro software, which provides a user-friendly environment for configuring, programming, and managing the PLC. Unity Pro's comprehensive features include advanced diagnostics and simulation capabilities, which help reduce development time and improve system reliability.
Products

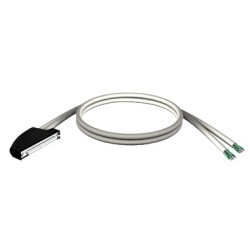

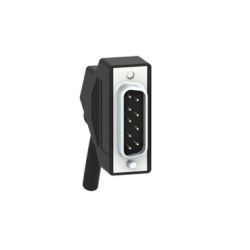
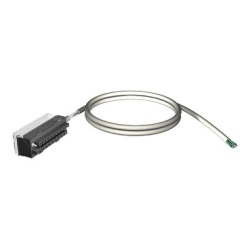
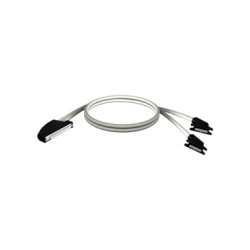
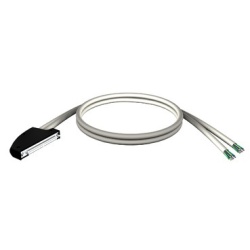
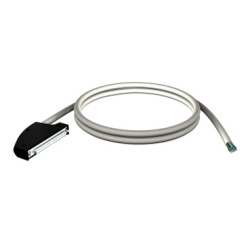
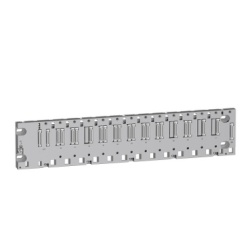
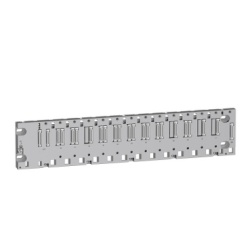

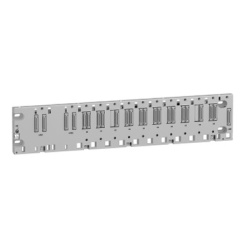
PLCs
Programming Logic Controllers (PLCs) are industrial computer that are designed to monitor and control a series of inputs and outputs.
The program running the PLC evaluates the inputs, and changes the output signals based on the program response to the input signals. Several programming languages are available to program most PLCs. The most common of these is called ladder logic. Ladder logic is a visual programming language that evolved from relay logic diagrams, which visually look like ladders because they consist of two vertical rails with runs between them that contain programmed logic. While ladder logic is the most common programming language used within PLCs, there are others that are also common, including function block diagrams, structured text and sequential function charts.
The hardware included in a PLC includes: a CPU, memory, I/O connections, a power supply and a programming device.
The CPU is a microprocessor that acts as the brains of the PLC. It performs logic operations, controls instruction and performs various other tasks that help keep the PLC running effectively. The memory in a PLC allows data to be stored that is needed to run the program, as well as any data that is collected by the inputs. Depending on the the type of PLC, the section for I/O may have a fixed number of points or it may be modular, allowing for additional I/O to be added. Many PLCs require some type of power supply and it is common to see more modular based systems integrate the power supply. Lastly, the PLC provides a programming device that feeds the program into the PLC's memory, so that it can perform the desired operation. This is most commonly some type of computer.
The PLC is designed to run a program repeatedly over and over again, normally many times a second. Each time a program runs, the PLC goes through some very specific steps.
While the order and the specifics may vary from manufacturer to manufacturer, they all typically follow a pattern similar to the following:
The PLC performs internal self checks to make sure that it is functioning correctly.
The PLC reads the inputs that are connected to it. It will then store the status of each of those inputs in its memory.
The PLC will execute the program logic.
The PLC will write the new values to the hard wired outputs to match those determined during the program execution. At some point in the cycle, communication requests will also be processed.
Following the execution of the last step, the PLC will then cycle back to the beginning of the process and begin all over again.