
Definite Purpose Contactors
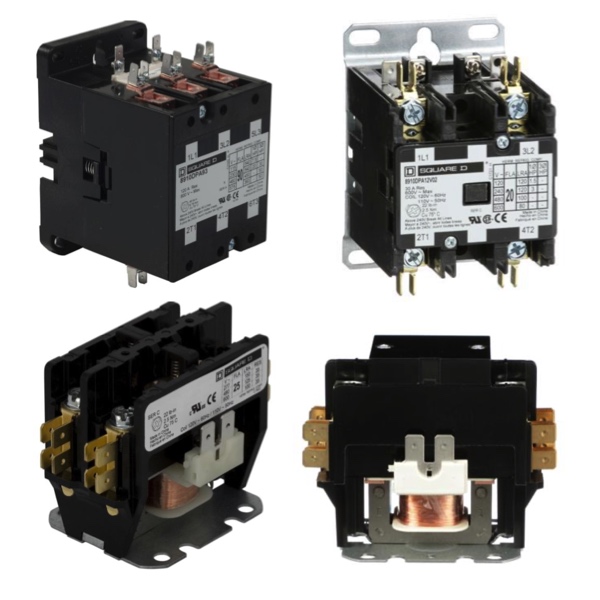
Definite purpose contactors are specialized electrical devices with certain applications, like HVAC equipment and refrigeration systems. They aren't general-purpose contactors, and they're not used in applications where reliable inrush current handling and frequent cycling performance are less critical. Compared to contactors with a general purpose, definite purpose contactors come in smaller packages, cost less, and are engineered with greater compatibility for use with compressors and heating/cooling systems.
These purpose-made definite contactors have quick connect terminals, and they have secure pressure-plate connections for easy wiring. They are made in multiple poles, in different contact configurations; and they're available in several coil voltages to fit specific needs. They have mechanical durability. They switch electrical loads efficiently, including shunt loads, and do it without compromising either performance or reliability.
Products
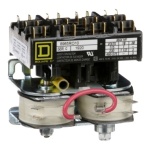
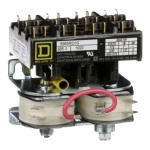
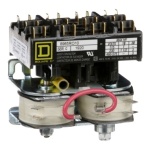
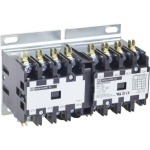
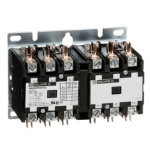

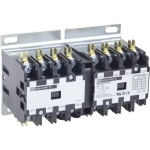
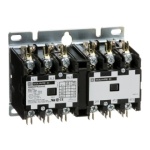

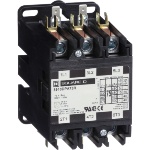
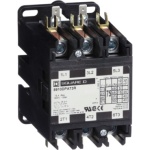
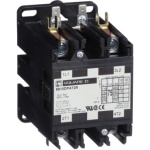
More Information about Definite Purpose Contactors
Intended for ongoing operation, DP contactors yield a low-price solution that is acceptable for the industry in need of reliable motor control and electrical switching. Their design mostly governs their efficiency and dependability—that is, effective switching within a wide variety of circuits. As a result, one will find these devices in a diverse range of applications, from simple on/off controls to complex reversing circuits. Their installation is straightforward, and they require virtually no maintenance, making them well suited to perform in an industrial capacity.
FAQs
What kind of resistive heating loads and load amps can a definite purpose contactor handle?
A definite purpose contactor can handle resistive heating loads typically ranging from a few amps up to several hundred amps, depending on the specific model and application requirements.
Are definite purpose contactors UL recognized for use in air conditioning applications?
Yes, definite purpose contactors are UL recognized and designed for air conditioning applications, ensuring reliable switching, motor control, and efficient operation in HVAC systems.
Motor Control Basics
Motor control allows operational control of electrical motors in various environments.
Motor control circuits provide a safe way to operate electrical motors. Back when motor control circuits were in their infancy, it would have been common to see a simple disconnect switch that would be used to turn on and off a motor. Depending on the size of the motor and how much voltage was required, operating this disconnect would have been dangerous, with a very high possibility of arcing or electrocution. Not to mention that when the disconnect was actuated, the large amount of inrush current would have damaged the motor over time.
In today's motor control circuits, there are a few common pieces of hardware.
A circuit breaker is used to protect the motor and any hardware downstream. A contactor and an overload relay are connected together and function in tandem to allow for remote and safe operation of the motor. The contactor functions much like a relay, allowing for a smaller electrical circuit to remotely close the motor contacts, starting the motor. The overload relay is designed to protect the motor in the case of a prolonged overcurrent event. These two devices are wired in series, so that if the overload relay detects an overcurrent event, the contactor will open the motor contacts, shutting off power to the motor.
The other two most common types of motor control hardware are a soft starter and a Variable Frequency Drive (VFD).
Both of these devices function in a similar way to the motor circuit with some added functions. The soft starter is designed to reduce large inrush current to the motor upon startup. This “soft starting” of the motor will prolong its life and allow for safer operation. The VFD performs the soft start functions, but also allows for speed control of the motor. This speed control is critical in many different environments and has made VFDs one of the most common and safe to use motor control circuits today.