
NEMA Reversing Contactors
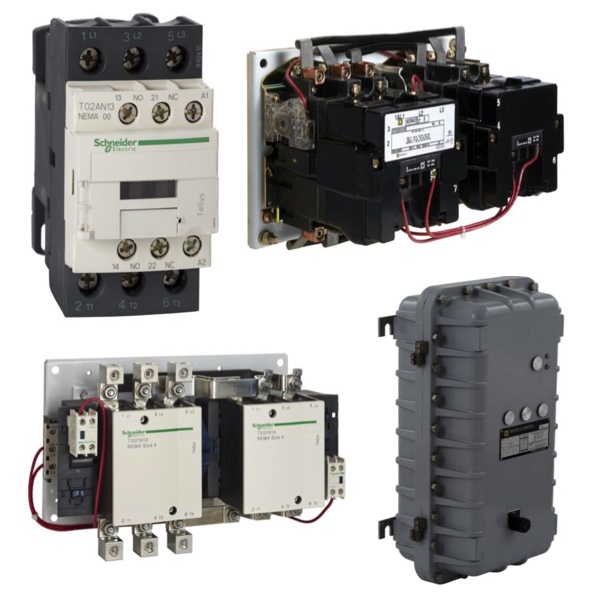
NEMA reversing contactors are designed for AC motors, providing full voltage control and enabling smooth motor direction switching. Electrically interlocked, these NEMA contactors assure that the forward and reverse circuits won't simultaneously engage to protect the motor and control system. Available in various NEMA sizes, including Size 00, the contactors permit selection on the basis of motor requirements. And while they don't furnish overload protection--that's typically provided separately--they do give you the flexibility to choose the right level of protection for your specific application.
These contactors come with interlocked components, both mechanical and electrical, that guarantee a reliable and safe performance. They are available in multiple options for coil voltage, thus they accommodate diverse configurations of power supplies. The contact loads handled by the poles are designed to take on different kinds of motor loads, and a variety of additional components makes it possible to tailor these devices to specific system needs. Certain contactor models are appropriate for use in marine environments and offer the durability that such conditions demand. Most contactors have an open-frame design that facilitates maintenance and an easy fit into control panels.
Products
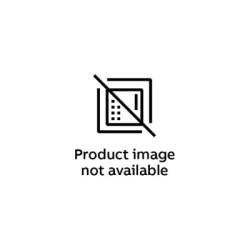
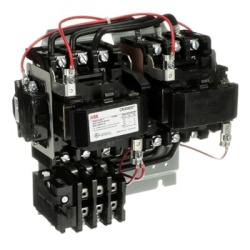
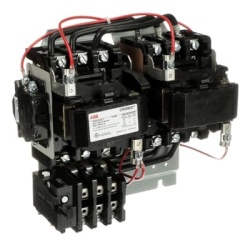
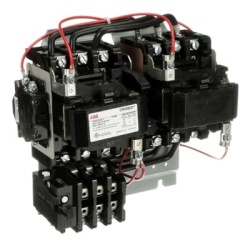
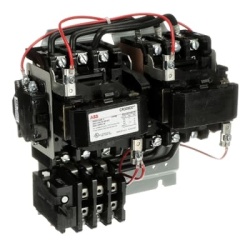
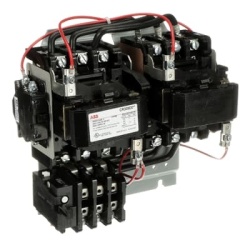
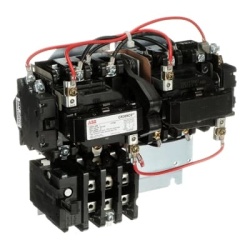
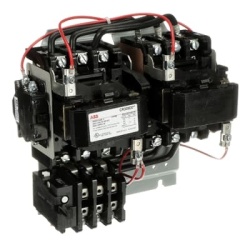
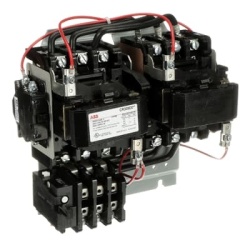
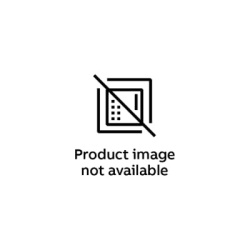

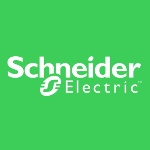
More Information about NEMA Reversing Contactors
NEMA reversing contactors guarantee effective motor direction switching and dependable overload protection in applications that range from manufacturing to the marine and from heavy to light duty. Their modular designs make them easy to integrate into existing systems and sure to meet the very high performance and safety demands of those three sectors. They come in various sizes, with several configurations, and the long-term durability necessary to put them in various applications in the three sectors.
FAQs
What type of frame size and housing is available in NEMA compliant reversing contactors?
NEMA compliant reversing contactors are available in a range of frame sizes from NEMA size 00 to size 9, and they typically feature durable housings made of materials such as steel or high-strength plastic to withstand industrial environments.
What accessories can one select to go with reversing contactors?
One can select accessories for reversing contactors, such as overload protection relays, auxiliary contacts, mechanical and electrical interlocks, coil voltage options, surge suppressors, and pilot devices to enhance control, safety, and functionality.
Motor Control Basics
Motor control allows operational control of electrical motors in various environments.
Motor control circuits provide a safe way to operate electrical motors. Back when motor control circuits were in their infancy, it would have been common to see a simple disconnect switch that would be used to turn on and off a motor. Depending on the size of the motor and how much voltage was required, operating this disconnect would have been dangerous, with a very high possibility of arcing or electrocution. Not to mention that when the disconnect was actuated, the large amount of inrush current would have damaged the motor over time.
In today's motor control circuits, there are a few common pieces of hardware.
A circuit breaker is used to protect the motor and any hardware downstream. A contactor and an overload relay are connected together and function in tandem to allow for remote and safe operation of the motor. The contactor functions much like a relay, allowing for a smaller electrical circuit to remotely close the motor contacts, starting the motor. The overload relay is designed to protect the motor in the case of a prolonged overcurrent event. These two devices are wired in series, so that if the overload relay detects an overcurrent event, the contactor will open the motor contacts, shutting off power to the motor.
The other two most common types of motor control hardware are a soft starter and a Variable Frequency Drive (VFD).
Both of these devices function in a similar way to the motor circuit with some added functions. The soft starter is designed to reduce large inrush current to the motor upon startup. This “soft starting” of the motor will prolong its life and allow for safer operation. The VFD performs the soft start functions, but also allows for speed control of the motor. This speed control is critical in many different environments and has made VFDs one of the most common and safe to use motor control circuits today.