
NEMA Non-Reversing Contactors
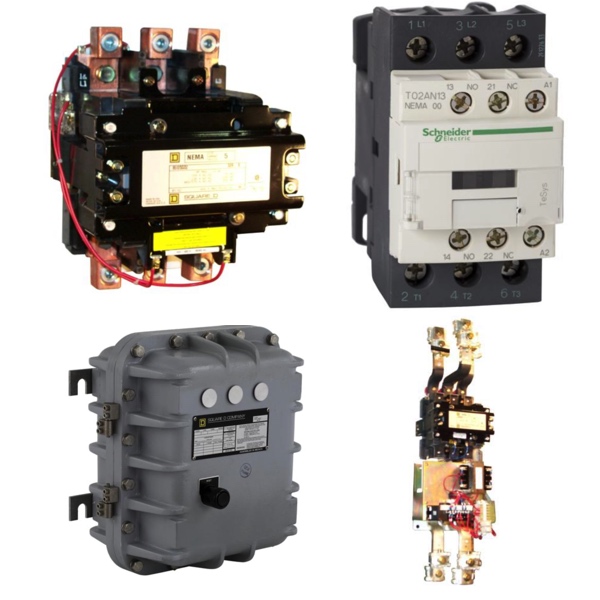
Non-reversing starter contactors are electrical devices commonly used to control the operation of electric motors in a single direction. They are distinct from reversing contactors that allow bidirectional motor control. Non-reversing contactors are typically connected to a power supply, which can be a circuit breaker or another power source. Wiring diagrams are available to guide the proper installation and connection of these contactors. They are designed for specific voltage ratings, such as 110-480 VAC at 50-60 Hz. Non-reversing contactors are not suitable for controlling motors that need to operate in the opposite direction.
NEMA non-reversing contactors are contactors that comply with the standards set by the National Electrical Manufacturers Association (NEMA) in the United States. NEMA is an industry association that establishes and publishes standards for electrical equipment and systems. NEMA non-reversing contactors are constructed to meet the rigorous requirements of industrial environments. They are built to withstand high currents, voltage fluctuations, and mechanical stress. The contactors are typically housed in rugged enclosures to protect the internal components from environmental factors and provide electrical insulation.
Products
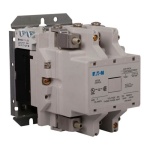
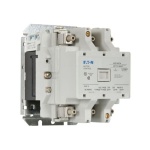

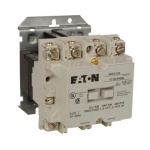




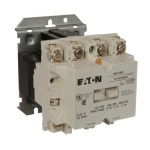
More Information about Non-Reversing Contactors
These contactors are used in various applications where motors need to rotate in only one direction. They can switch heating loads and supply power to the motor in a single direction. Non-reversing contactors are available in different NEMA sizes, indicating their physical dimensions and mounting characteristics. Overload protection is an important consideration to prevent motor damage due to excessive current, and some contactors include auxiliary contacts for additional control functions or signaling purposes.
The current rating of non-reversing contactors determines their maximum current-handling capacity without overheating or malfunctioning. Coil voltage refers to the voltage required to energize the contactor's coil and activate the switching mechanism. Contactors come in various sizes, with larger ones capable of handling higher currents. They are commonly used in motor control applications across industries, either provided separately or as part of a motor control assembly.
When energized, non-reversing contactors allow power to flow to the motor in the specified direction. They are designed by different manufacturers, offering various details and specifications to meet specific application requirements. Compatibility with other control devices, such as relays or timers, should be considered for proper integration into the system. Non-reversing contactors are categorized based on their intended use, such as industrial, commercial, or residential applications.
Reviews and ratings can assist in the decision-making process when selecting non-reversing contactors for a project. Depending on the specific motor control requirements, additional components like fuses, transformers, or capacitors may be needed. Non-reversing contactors typically have multiple poles to handle the necessary switching connections for the motor and control circuits.
Motor Control Basics
Motor control allows operational control of electrical motors in various environments.
Motor control circuits provide a safe way to operate electrical motors. Back when motor control circuits were in their infancy, it would have been common to see a simple disconnect switch that would be used to turn on and off a motor. Depending on the size of the motor and how much voltage was required, operating this disconnect would have been dangerous, with a very high possibility of arcing or electrocution. Not to mention that when the disconnect was actuated, the large amount of inrush current would have damaged the motor over time.
In today's motor control circuits, there are a few common pieces of hardware.
A circuit breaker is used to protect the motor and any hardware downstream. A contactor and an overload relay are connected together and function in tandem to allow for remote and safe operation of the motor. The contactor functions much like a relay, allowing for a smaller electrical circuit to remotely close the motor contacts, starting the motor. The overload relay is designed to protect the motor in the case of a prolonged overcurrent event. These two devices are wired in series, so that if the overload relay detects an overcurrent event, the contactor will open the motor contacts, shutting off power to the motor.
The other two most common types of motor control hardware are a soft starter and a Variable Frequency Drive (VFD).
Both of these devices function in a similar way to the motor circuit with some added functions. The soft starter is designed to reduce large inrush current to the motor upon startup. This “soft starting” of the motor will prolong its life and allow for safer operation. The VFD performs the soft start functions, but also allows for speed control of the motor. This speed control is critical in many different environments and has made VFDs one of the most common and safe to use motor control circuits today.