
Wire Sleeving
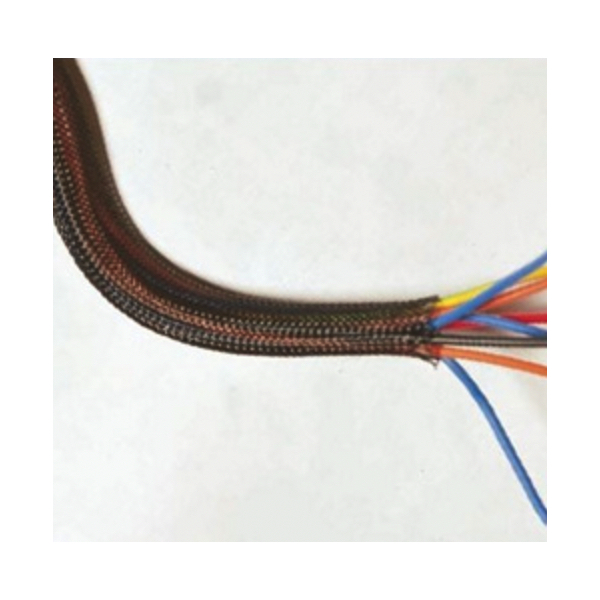
When wires and cables need protection, they can be encased in wire sleeving, which serves as a kind of armor against a wide range of potential hazards: wires rubbing together, their insulation melting under excessive heat, common chemicals that erode so many materials, and any of sundry environmental aggressors that may be present.
There are many types of wire sleeving you can choose for your project, but three of the most common are braided, spiral, and heat shrink tubing. Each has its own advantages and is suitable for different applications. When it comes to flexibility and ease of use, it's hard to beat braided sleeving. Expandable braided sleeving can handle a wide range of diameters and can expand to fit over bulky fittings and connectors and around odd shapes.
Products
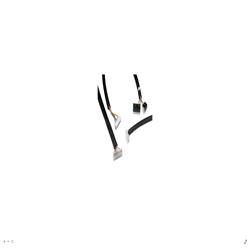
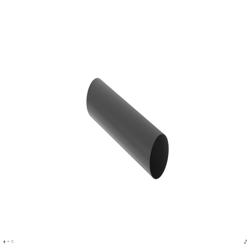
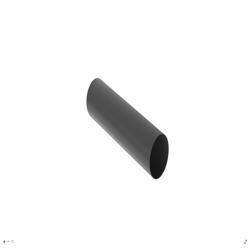
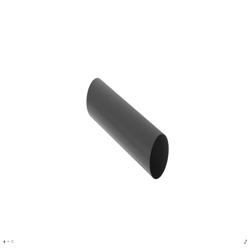
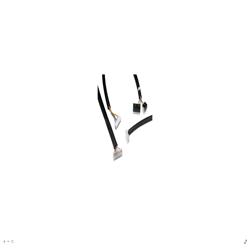
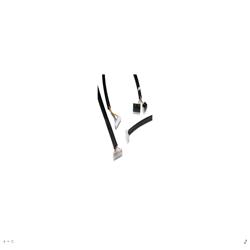
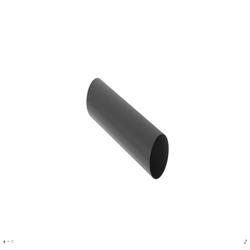
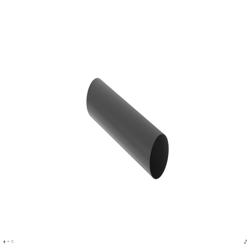
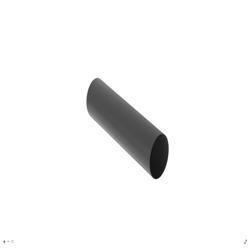
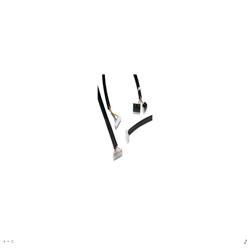
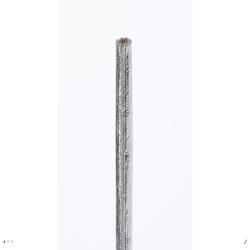
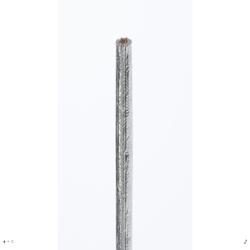
More Information about Wire Sleeving
Braided expandable sleeving is a protective cover that is specifically designed keeps wires and cables together and safe from the many hazards they might face. The sleeving is usually made from different kinds of materials, like polyester, that are meant to keep the wires from rubbing against each other or from rubbing against another surface. This is important because abrasion can lead to an electric arc or fire, with potentially devastating consequences.
FAQs
Does braided cable sleeving protect cables from being damaged in automotive applications?
Yes, braided cable sleeving protects cables from damage in automotive applications by offering ideal resistance to abrasion, heat, and chemicals while providing flexibility and durability.
Does wire bundling in polyethylene terephthalate provide any flame retardant features?
Yes, wire bundling in polyethylene terephthalate (PET) can provide flame retardant features, as PET sleeving is often treated to meet various flame retardancy standards, enhancing safety in electrical installations.
Tips for Exceptional Wire Management
Be consistent.
This is one of the most overlooked aspects of great wire management. Consistency should apply to everything including the length of wire that is being used, the bend radius of the wire, the wire placement within the bundles and the label positions.
Don't always take the shortest path.
When routing wires and trying to achieve a clean and organized look, it is important to not always take the shortest route to land the wires. For example, when wiring hardware on the door of an electrical enclosure it is important to consider all of the wires that are going to be at that location and bundle these wires whenever possible. Instead of just running the wires directly to the place that they need to be connected, route the wires in a way that will pass other devices or connection points near the wire and pick up any other wires along the way that are related to those other connection points.
Wire tie everything that is not concealed.
When wiring in a control panel, the wires are often concealed by the wire ducting. However, there are times when wires are not concealed and are difficult to control in such a way that will result in a clean and organized look. To assist with this problem, it is important to use wire ties and wire tie anchors. Make sure that the same size wire tie and the same color is used throughout the install process.