
Enclosure Backplates
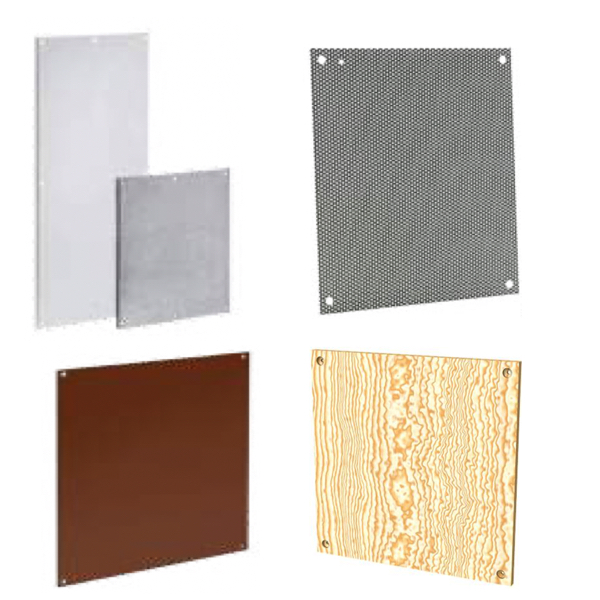
Enclosure backplates are offset from the back of the enclosure allowing electrical devices to be mounted without compromising the integrity or NEMA rating of the enclosure. Most backplates come with pre-cut holes to match the mounting holes in the enclosure. These interior backplates can also be removed or replaced, allowing the components to be easily worked on, without uninstalling the entire electrical cabinet. Backplates are made of steel, fiberglass, aluminum, wood, galvanized steel, painted steel, as well as composite materials.
Allied Moulded enclosure backplates are available in aluminum, fiberglass, galvanized steel, PVC and white painted carbon steel.
Hoffman Composite Backplates are manufactured from reinforced phenolic laminate sheet stock, which has exceptional strength and chemical resistance. Composite backplates can be drilled and tapped and are intended for use in corrosion-resistant enclosures.
Products
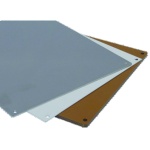
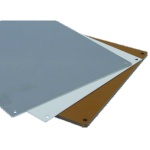
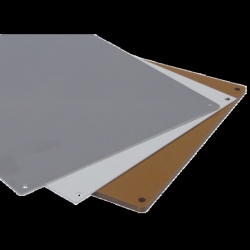
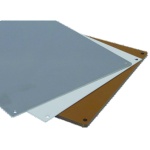
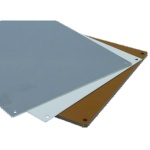
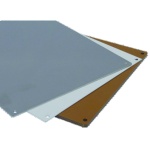
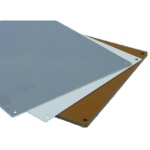
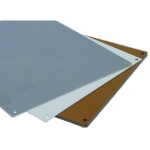
More Information about Enclosure Backplates
Hoffman Backplates for Type 3R, 4, 4X, 12 and 13 enclosures are aluminum, painted steel or Type 316 stainless steel. Some larger backplates have flanges on two or four sides and include extra holes for backplate lifting.
Hoffman Backplates for free-stand single and dual access one-door enclosures are 12 gauge painted steel and can be positioned anywhere along the horizontal mounting channels. Half-length back panels can be located in the upper and lower portion of the enclosure.
Hoffman Backplates for WiFi cabinets are available in either 14 gauge painted steel or ¾ inch plywood. Wood backplates are supplied with POLYPRO Type 4X WiFi cabinets and Fiberglass Hinged-Cover cabinets.
Panel Build Series Part 14: Drilling and Tapping
Drilling and tapping holes into a steel back plane for hardware attachment.
Take inventory of the tools needed for the job.
A metal punch is used to make a small divot in the metal so that the drill bit won't wander, a very sharp machine drill bit and a 10-24 tap. The size of the bit and tap will depend on the type of hardware being used to secure the din rail and wire ducting to the panel.
Punch to create divots on previously marked layout.
Always punch before drilling and make sure that the punch is in the center of the mark.
Drilling into the steel back plane.
Make sure that the drill bit is very sharp, use lubrication to prolong the life of the bit, place the bit into the punched divot and start drilling. Clean up any metal shards when drilling is complete.
Tapping the holes to create threads.
Make sure that the tap is very sharp and lubrication is used when tapping the holes. Do not over torque the tap which can cause it to break. Make sure that the tap goes completely through the hole until it turns easily to ensure that the holes have been properly threaded. Test the threaded holes with a screw. Clean up any metal shards. The back plane is now ready for mounting hardware.