
Pressure Sensors & Transmitters
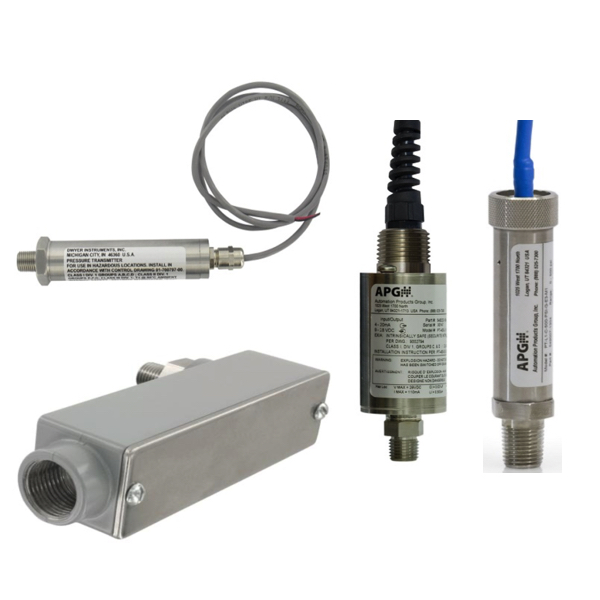
Pressure sensors and transmitters are devices used in many industries to measure and monitor the pressure of gases and liquids. When a pressure sensor is used, a change in pressure causes the sensor to react and convert the pressure change into an electrical signal. This electrical signal can then be used to collect data or for real-time control of a system. In hydraulic systems and HVAC applications, for example, pressure sensors do essential work that ensures the proper operation of the systems they monitor. Pressure transmitters take the measured pressure and convert it into output signals that can be transmitted to the systems monitoring and controlling industrial processes.
There are many configurations for these different devices, including sensors that measure the pressure difference between two points (differential pressure sensors) and a kind of pressure sensor that is very accurate and that works well in a wide variety of environments (pressure transducers). In harsh environments, these devices provide trustworthy measurements, due to their heavy-duty stainless steel construction.
Products
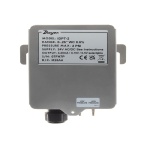
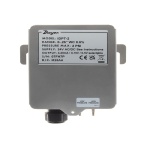
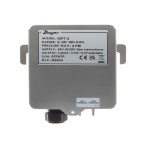
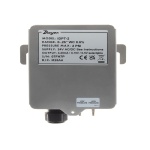
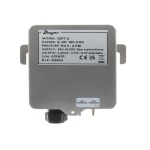
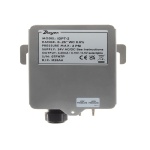
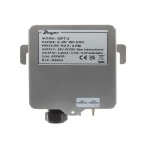
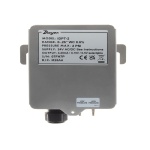
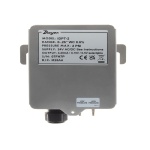
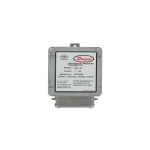
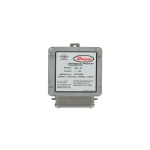
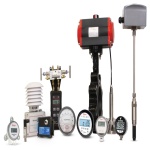
More Information about Pressure Sensors and Transmitters
Across a wide swath of demanding applications, pressure sensors and transmitters are used to great effect. They are built both in compact versions, for use in space-limited environments, and in rugged formats, for use in punishing conditions. Their high accuracy, outstanding durability, and versatility across an extensive range of pressures make them a critical component of safe and efficient operations almost anywhere in the industrial sector. Pumps, compressors, and clean rooms (among many other applications) use pressure devices to manage systems effectively and to deliver electrical signals that keep them running smoothly.
Instrumentation: Elements & Transmitters
2 pieces of hardware used in modern day instrumentation: measuring elements and transmitters.
Measuring Elements
Measuring elements are the part of the device that performs the measurement. For example, the measuring element of a pressure transducer is the part that is actually lowered into a tank that will take a pressure measurement. The measuring element of a flow meter is the part that actually measures the flow and an RTD or thermocouple takes the temperature measurement.
Transmitters
Transmitters collect information from measuring elements and sends the information to where it is needed. The transmitter interfaces with the measuring element and interprets the information. It then sends that information to a PLC, RTU or some other type of control unit. In many cases, the transmitter has the ability to communicate the information via multiple communication protocols. This may be necessary when the measuring element does not send the same type of signal that is needed by the controller. For example, it may be necessary to convert a temperature reading from a thermocouple to a 420 milliamp signal that can be received by a local PLC.