
Cable Strain Relief

Cable strain relief is an essential part of electrical and electronic systems because it protects the cables inside those systems from being damaged. They can become damaged if they are under a lot of stress, are bent too far, or if someone tries to pull them out of an assembly. When one of these things happens, you can consider this a failure event—because it saps the intended energy from the system, in the case of a power cable, or corrupts the signal, or worse, causes whatever's happening in the cables to stop happening, in the case of conductive cable.
A variety of materials can produce stress relief devices. Designers can turn to plastic, metal, or rubber to mold devices suited to a cable stress problem. The methods and materials used in stress relief can be easily and cheaply scaled for mass production. Cord grips and cable glands are types of stress relief devices that could seemingly house just about any cable size, making these the workhorses in today’s market. Once properly installed, relief cord grips also are very reliable in giving operators the opportunity to move and manipulate their attached cables when the time comes.
Products
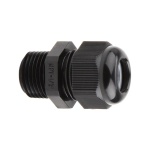
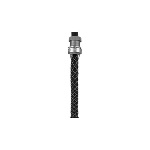
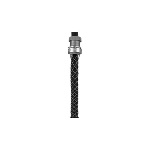
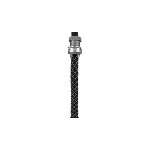
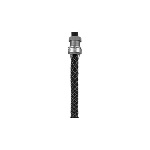

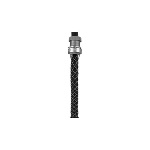
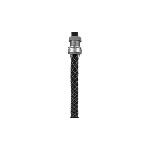
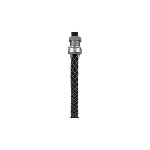
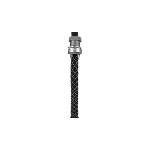
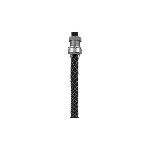

More Information about Cable Strain Relief
Installing strain relief is a simple process that usually entails clamping or fastening the device securely around the cable, right at the point where the cable enters the connector housing. This step enhances cable life and reliability, but it also has the added benefit of improving overall cable system safety. When the cable isn't under much strain, it can easily be pulled from where it's inserted and cause a total or partial system shutdown. When strain is applied to the cable, if the cable has effective strain relief installed, then the force should be mostly (if not entirely) relieved on the cable at the point where it's intended to be relieved.
FAQs
Is a nickel plated brass cable gland the best stress relief option for control cabinets?
Yes, a nickel-plated brass cable gland is an excellent stress relief option for control cabinets due to its durability, corrosion resistance, and ability to provide a secure and reliable seal in industrial environments.
Tips for Exceptional Wire Management
Be consistent.
This is one of the most overlooked aspects of great wire management. Consistency should apply to everything including the length of wire that is being used, the bend radius of the wire, the wire placement within the bundles and the label positions.
Don't always take the shortest path.
When routing wires and trying to achieve a clean and organized look, it is important to not always take the shortest route to land the wires. For example, when wiring hardware on the door of an electrical enclosure it is important to consider all of the wires that are going to be at that location and bundle these wires whenever possible. Instead of just running the wires directly to the place that they need to be connected, route the wires in a way that will pass other devices or connection points near the wire and pick up any other wires along the way that are related to those other connection points.
Wire tie everything that is not concealed.
When wiring in a control panel, the wires are often concealed by the wire ducting. However, there are times when wires are not concealed and are difficult to control in such a way that will result in a clean and organized look. To assist with this problem, it is important to use wire ties and wire tie anchors. Make sure that the same size wire tie and the same color is used throughout the install process.