
Harmonic & SineWave Filters for VFDs
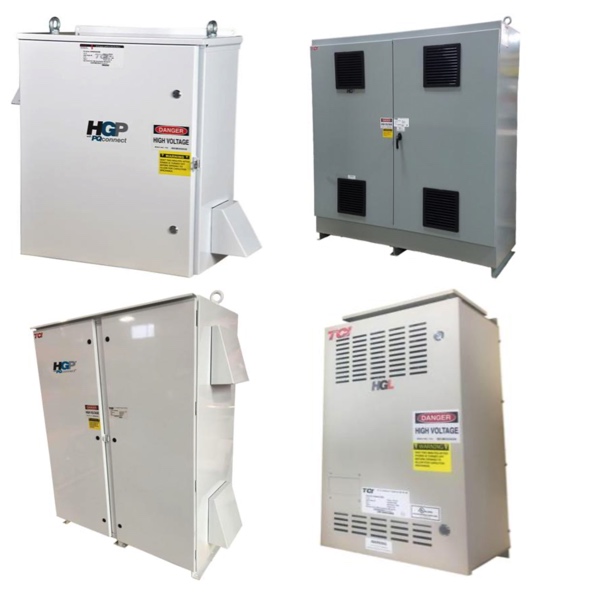
For variable frequency drives (VFDs), filters are essential components. They greatly contribute to the VFD's and connected motor's reliability, performance, and service life. These devices address problems like electromagnetic interference (EMI), harmonic distortion, and voltage spikes that can affect not only the drive but also surrounding equipment.
Harmonics are unwanted components that degrade the electrical waveform—the very thing we think of as "electrical power"—and they can cause all sorts of problems, from overheating transformers and motors to making sensitive equipment malfunction. A must-have for any VFD is a harmonics filter: an electrical component that keeps the VFD away from its neighbors and makes the whole system work more efficiently. Harmonic filters do the opposite of what harmonics do: they make certain frequencies go away, which keeps the power clean.
The sine wave filter is a conversion device that takes the pulse-width modulated (PWM) output from variable frequency drives (VFDs), and with it, gives rise to a sinusoidal waveform. This type of filtered output is necessary to ensure not only reliable but also efficient operation of electric motors—particularly those with long cables or in applications where the motor's sensitive components are prone to frequencies deemed undesirable.
Products
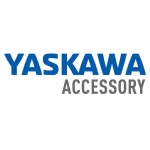

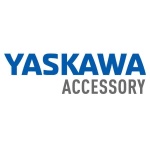
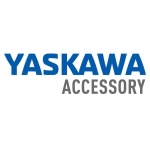
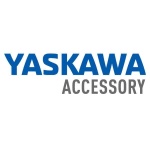
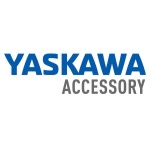
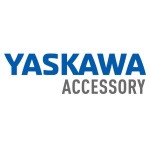
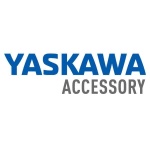
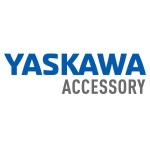
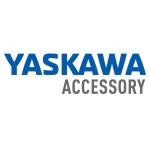
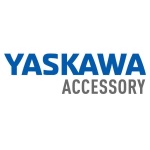
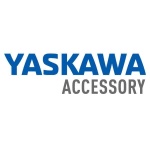
More Information about Harmonic & SineWave Filters for VFDs
Passive harmonic filters are highly effective at improving the efficiency and lifespan of electrical equipment. By reducing harmonic distortion, they help prevent overheating, vibrations, and other stresses on transformers, motors, and generators. Passive filters rely solely on passive components, therefore they do not require an external power system or active control mechanisms, making them inherently robust and low-maintenance.
FAQs
Does a passive harmonic filter improve switching frequency, harmonic currents and harmonic frequencies, thus improving the power quality?
A passive harmonic filter improves harmonic currents and reduces harmonic frequencies, thereby improving power quality, but it does not directly affect the switching frequency of the variable frequency drive.
Do sine wave filters have a power factor correction for power systems?
No, sine wave filters do not provide power factor correction; their primary function is to smooth the PWM output from variable frequency drives into a sinusoidal waveform, reducing harmonics and protecting motors.
Inductive Load Basics
Electrical load is an electrical component or portion of a circuit that consumes electrical power. For example, a power source such as a battery or generator will have a load which consumes that power, such as a light bulb, motor or television.
There are three types of electrical loads: capacitive loads, resistive loads and inductive loads
Capacitive and Resistive Loads
Capacitive loads are similar to inductive loads in that the current and voltage are out of phase with one another, however, capacitive loads see the current reach its maximum before the voltage, while inductive loads see the voltage reach its maximum before the current. Resistive loads typically consist of things like heating elements.
Inductive Loads
Inductive loads use a coil to produce a magnetic field. The most common types of inductive loads are motors, fans, blenders and pumps. Inductive loads resist change in current, which lags behind the voltage. There are two different types of power with inductive loads. There is real power, which is based off of the work that is actually being done by the motor and there is reactive power, which is the power that is drawn from the power source to produce the magnetic field. The total power of an inductive load combines both the real power and reactive power.