
COMPACT Enclosure Accessories
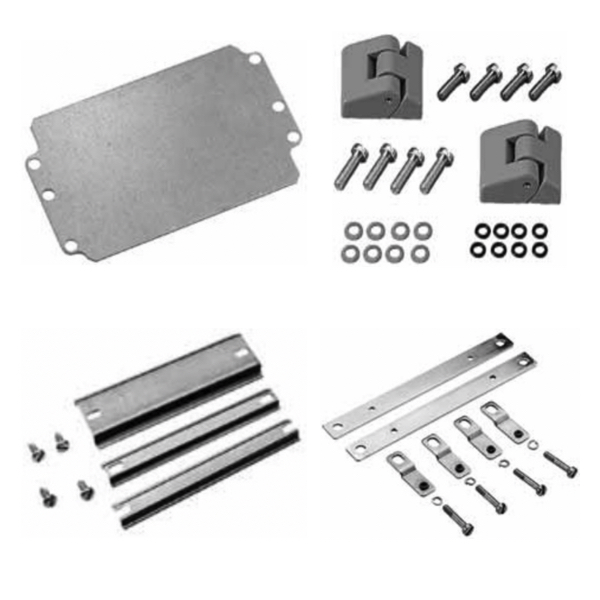
Hoffman COMPACT aluminum enclosures protect controls and components for indoor and outdoor applications in corrosive environments. COMPACT accessories include: Hinge kits made of die-cast aluminum with an angle rotation of approximately 170 degrees. Two hinges, mounting template and stainless steel hardware are included. Mounting bracket kits include two or four brackets made from 12 gauge steel alloy providing enhanced corrosion resistance. Panels made of plated steel permits electromechanical components to be mounted inside the enclosure. DIN type rails made of plated steel and receive relays, terminal blocks, switches, timers, filters and various other electrical components.
Products

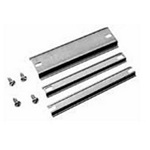




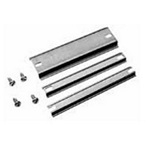

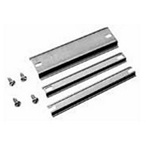



More Information About COMPACT Enclosure Accessories
Aluminum enclosures have many physical characteristics that make it an excellent choice for many industrial environments. Aluminum has a high strength-to-weight ratio, which means that it will maintain its shape when subjected to strong forces but with the added benefit of being lightweight. It also has a natural resistance to corrosion, making it an excellent choice for wet environments. Aluminum can dissipate heat, which can help to reduce the interior temperature of an enclosure housing components that can be damaged by high temperatures. And finally, aluminum enclosures are ideal for electronic and electrical equipment because of it does not react to magnetic forces, shielding internal components from radio frequency (RF) and electromagnetic frequency (EMF) interference. Aluminum enclosures can be found in water treatment facilities, marine environments and telecommunication settings.
Panel Build Series 14: Drilling and Tapping
Drilling and tapping holes into a steel back plane for hardware attachment.
Take inventory of the tools needed for the job. A metal punch is used to make a small divot in the metal so that the drill bit won't wander, a very sharp machine drill bit and a 10-24 tap. The size of the bit and tap will depend on the type of hardware being used to secure the din rail and wire ducting to the panel.
Punch to create divots on previously marked layout. Always punch before drilling and make sure that the punch is in the center of the mark.
Drilling into the steel back plane. Make sure that the drill bit is very sharp, use lubrication to prolong the life of the bit, place the bit into the punched divot and start drilling. Clean up any metal shards when drilling is complete.
Tapping the holes to create threads. Make sure that the tap is very sharp and lubrication is used when tapping the holes. Do not over torque the tap which can cause it to break. Make sure that the tap goes completely through the hole until it turns easily to ensure that the holes have been properly threaded. Test the threaded holes with a screw. Clean up any metal shards. The back plane is now ready for mounting hardware.